CRF Controlled Release Fertilizer Production Line Design
In today’s pursuit of efficient, eco-friendly, and sustainable agriculture, Controlled-Release Fertilizer (CRF) has become pivotal for modern farming upgrades due to its “precision-controlled release and long-lasting nutrient supply”. The core enabler of this technology is the high-efficiency, intelligent Controlled Release Fertilizer production line.
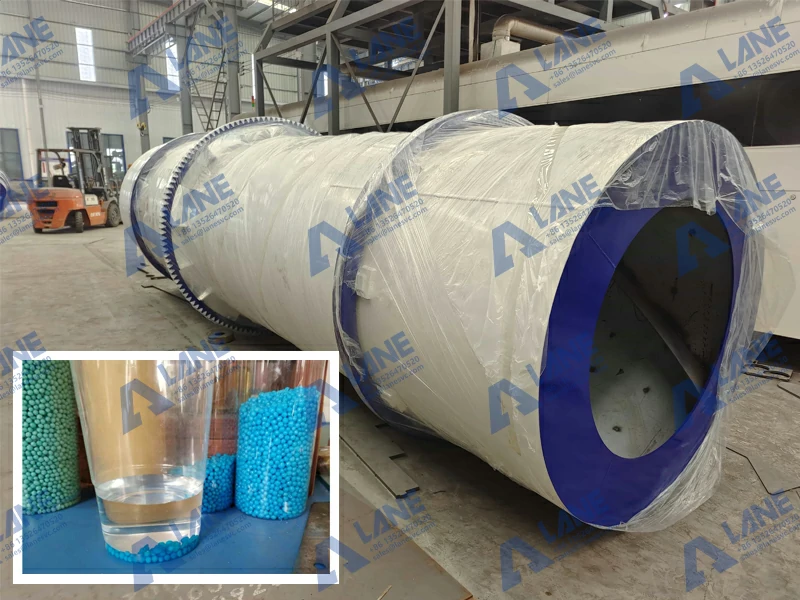
1. Core Raw Materials of Controlled Release Fertilizer Production Line
An advanced controlled release fertilizer production line can flexibly process a variety of raw material combinations:
Base fertilizers:
- Nitrogen sources: such as urea, ammonium sulfate, ammonium nitrate, etc.
- Phosphorus sources: such as monoammonium phosphate, diammonium phosphate, calcium superphosphate, etc.
- Potassium sources: such as potassium chloride, potassium sulfate, etc.
- Compound fertilizer granules: Pre-granulated NPK compound fertilizer granules serve as the core carrier.
Coating/controlled release materials: These are key to enabling the controlled release of fertilizer nutrients:
- Polymers: Such as thermoplastic resins, thermosetting resins (e.g., alkyd resins, polyurethanes, etc.), which are the most widely used coating materials.
- Sulfur: Commonly used for sulfur-coated urea.
- Inorganic compounds: Such as magnesium ammonium phosphate, which forms an insoluble layer through chemical reactions to achieve controlled release.
- Additives: Including solvents, plasticizers, crosslinking agents, pigments, fillers, etc., used to adjust coating performance, color, or reduce costs.
- Binders: Used in some processes to enhance the adhesion between the coating layer and fertilizer granules.
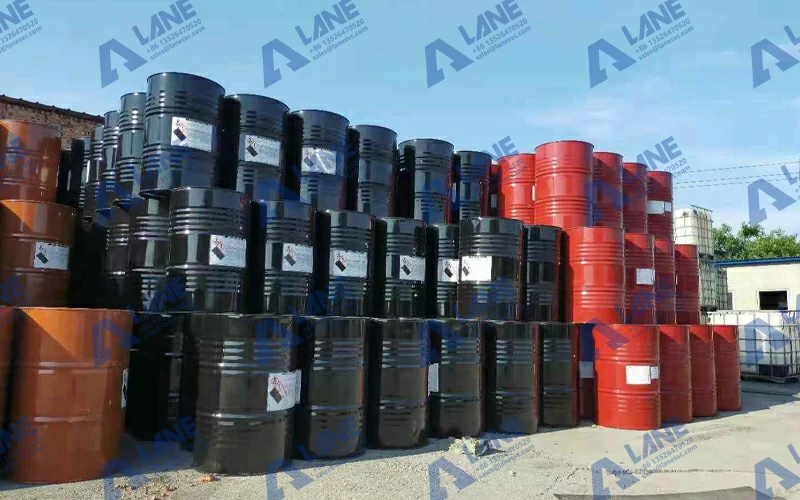
Coating solution
2. Features of controlled release fertilizer
- Precise controlled release: The release rate of fertilizer nutrients is highly matched with crop nutrient requirements, avoiding waste.
- Long-lasting nutrient supply: A single application of fertilizer meets most of the nutrient needs of crops throughout their entire growth period or key growth period, significantly reducing the number of additional fertilizations required, saving labor and effort.
- High-efficiency utilization: Significantly reduces nutrient volatilization, leaching, and fixation, with nitrogen fertilizer utilization rates improved by 30%-50%, effectively conserving resources.
- Environmentally Friendly: It greatly reduces the risk of nitrate pollution to groundwater, rivers, and lakes, alleviating agricultural non-point source pollution.
- Increased Yield and Improved Quality: Stable and balanced nutrient supply promotes healthy crop growth, increasing yield and improving the quality of agricultural products.
- Labor and Cost Savings: It reduces the number of fertilization applications, lowering labor and machinery costs.
3. Introduction to Controlled Release Fertilizer Production Line Main Equipment
A typical controlled release fertilizer production line usually includes the following steps and equipment:
1. Pre-treatment Section:
- Crusher: Crush large pieces of raw material or clumped fertilizer to the required particle size.
- Vibrating Screener/Rotary Screener: Screen the base fertilizer particles to remove powder and oversized particles, ensuring uniform particle size consistency for the coating process (function: ensure uniform coating and product quality stability).
- Elevator/Conveying Equipment: Convey materials between various equipment.
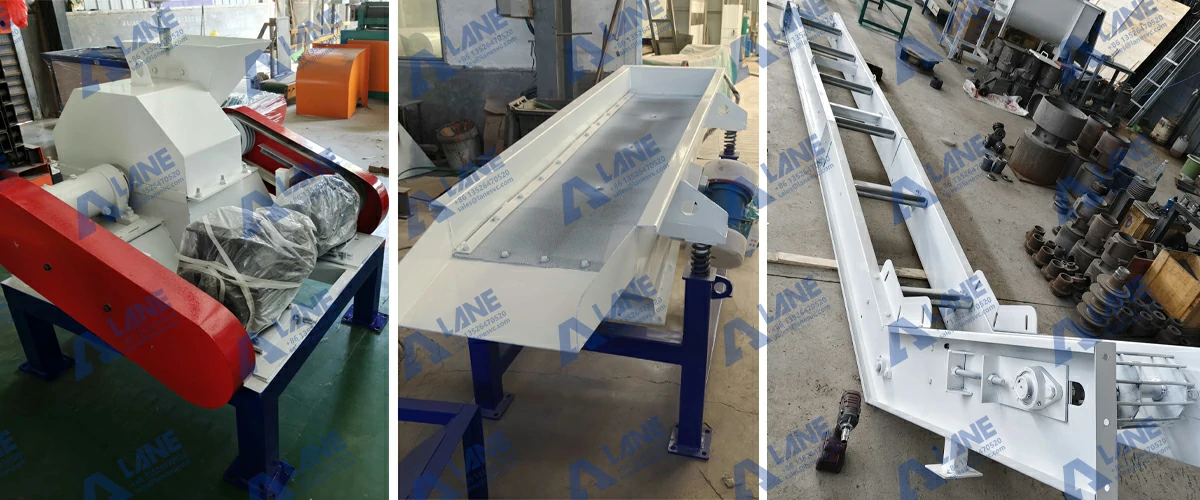
Cage crusher & Vibrating screener & Belt conveyor
2. Batching and Mixing Section:
- Raw Material Silos: Store various types of base fertilizer raw materials.
- Automatic Batching System: Precisely measure and blend various base fertilizer raw materials (function: ensure the nutrient content of the finished fertilizer meets specifications).
- Mixer (e.g., twin-shaft paddle mixer, drum mixer): Thoroughly mix the blended base fertilizer raw materials to achieve uniformity (function: ensure even distribution of nutrients between particles).
3. Controlled Release Fertilizer Production Line Granulation Section:
- Granulator (e.g., rotary granulator, disc granulator, extrusion granulator): Forms granules from uniformly mixed powdered base materials through processes such as agglomeration, extrusion, or melt cooling (function: prepares base fertilizer granules meeting coating requirements).
- Dryer (e.g., rotary dryer, fluidized bed dryer): Remove excess moisture from the granules after granulation (function: enhance granule strength and provide a dry surface for coating).
- Cooler (e.g., rotary cooler, fluidized bed cooler): Cool the high-temperature dried granules to near room temperature (function: prevent hot granules from clumping, facilitating subsequent coating and storage).
- Screener: Grades the granules after granulation, drying, and cooling. Qualified granules proceed to the coating process, fine powder is returned to granulation, and large granules are crushed (function: ensures that granules entering the coating section meet particle size requirements and are uniform).
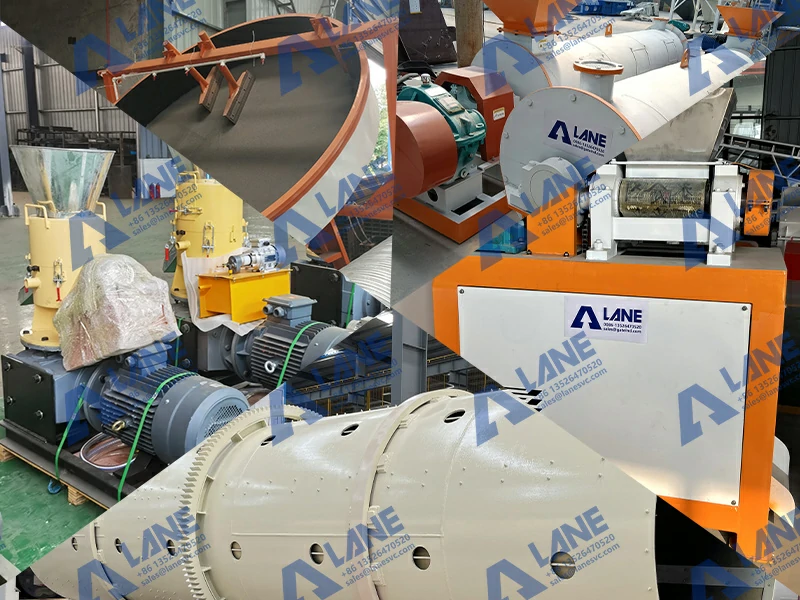
4. Controlled Release Fertilizer Production Line Coating Section (Core):
- Coating Machine (Core Equipment): Typically uses a drum coating machine. Its core is a rotating inclined drum.
- Function: Fertilizer granules continuously roll within the drum. Coating material (such as molten resin solution or suspension) is uniformly sprayed onto the granule surface via a precision spray gun system. The drum’s rotation and internal paddle design ensure thorough mixing of granules and formation of a uniform, continuous coating layer. Hot air can be introduced to promote solvent evaporation or resin curing.
- Coating solution preparation and supply system: Includes a dissolution tank, storage tank, heating system, filter, metering pump, spray gun (atomization device), etc.
- Function: Precisely prepare, store, heat, filter, meter, and atomize the coating material solution for spraying.
- Hot air system: Supplies hot air at a controlled temperature and flow rate into the coating machine.
- Function: Accelerates solvent evaporation in the coating material and/or promotes resin melting, leveling, and curing to form a dense film layer.
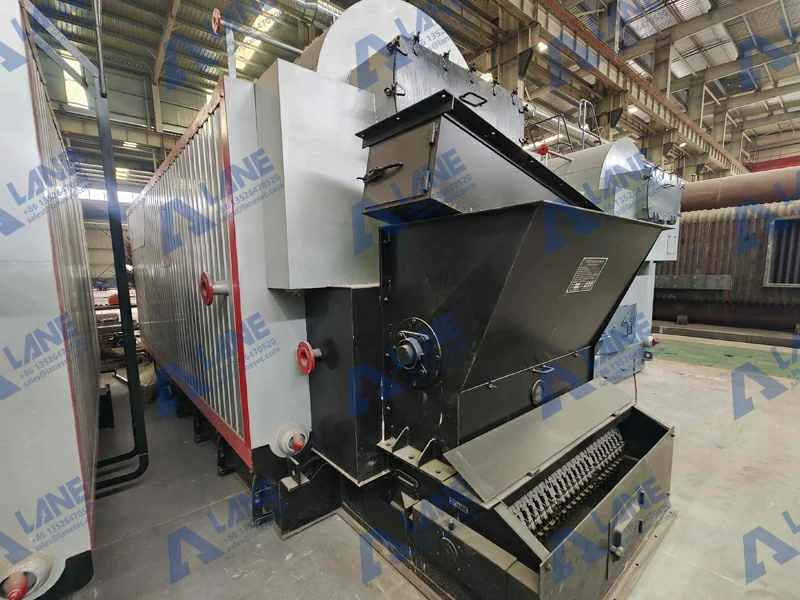
5. Controlled Release Fertilizer Production Line Curing/Post-Treatment Section:
- Curing Equipment (e.g., fluidized bed dryer/curing bed, cooling chamber): Coated particles typically require further processing to fully cure and set the film layer.
- Function: By controlling temperature and time, the coating layer is brought to its final stable state, ensuring its controlled release performance.
- Cooling Machine: Cools the cured particles to a safe storage temperature.
- Function: Prevents hot particles from clumping, ensuring product stability.
- Post-Screening Machine: Removes any small amounts of powder or agglomerated particles generated during the coating process.
- Function: Ensures the appearance quality and flowability of the finished product.
6. Finished Product Processing Section:
- Coating Agent/Anti-Caking Agent Spray Equipment: Sprays a minimal amount of anti-caking agent onto the surface of finished particles.
- Function: Enhances product flowability and anti-caking performance during storage.
- Automatic Packaging Scale and Packaging Line: Weighs, bags, and seals finished products.
- Palletizing Robot/Device: Automatically stacks packaged products neatly.
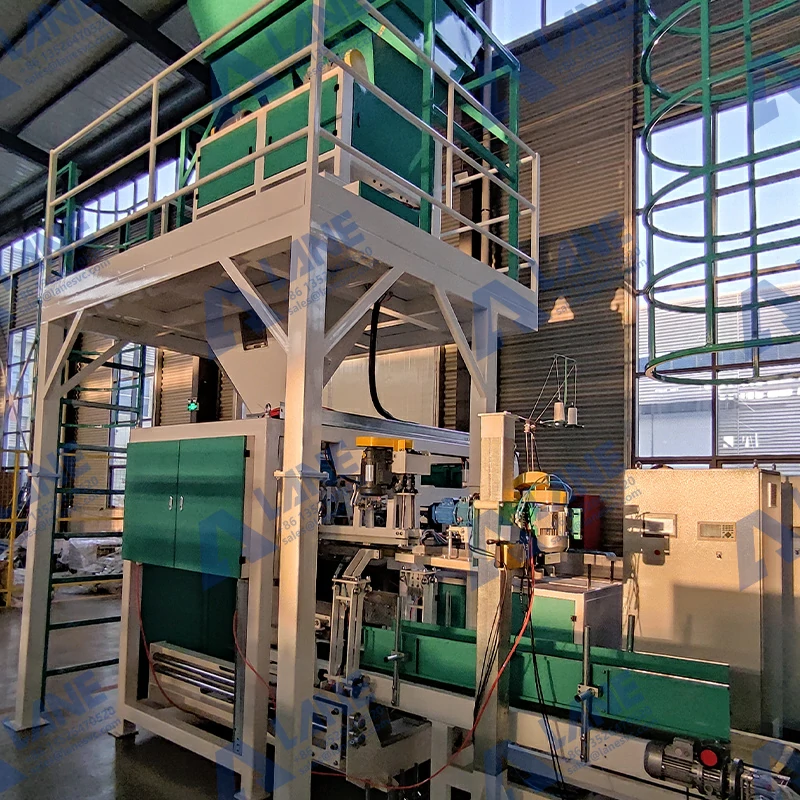
7. Control System in Controlled Release Fertilizer Production Line:
- Central Control System (PLC/DCS): Integrates automated instruments, sensors, and actuators.
- Function: Enables real-time monitoring, automated control, and data recording of key process parameters (temperature, flow rate, speed, material level, ratio, weight, etc.) across the entire production line, ensuring stable, efficient production and consistent product quality. It serves as the “brain” of modern controlled release fertilizer production lines.
4. Controlled release fertilizer production line process principle: precise coating, intelligent release
The core process of the controlled release fertilizer production line lies in uniform coating:
- Pre-treatment and particle preparation: Ensure that the base fertilizer particles are uniform in size and have clean, dry surfaces.
- Precision Spraying: In the drum coating machine, the granules are continuously tossed and rolled, while the coating material is uniformly applied to their surfaces via precision atomization spray guns.
- Film Formation and Curing: Under the influence of hot air, the solvent evaporates or the resin melts, flows, and cross-links to form a dense, semi-permeable membrane with a specific microporous structure on the granule surfaces.
- Controlled-release mechanism: This membrane acts as an “intelligent switch” for nutrient release. Water permeates through the microporous structure to dissolve internal nutrients, creating osmotic pressure. The nutrient solution then slowly and continuously diffuses through the microporous structure into the soil. The release rate is determined by factors such as the properties of the membrane material, membrane thickness, number and size of microporous structures, and environmental temperature and humidity, thereby achieving alignment with crop nutrient requirements.
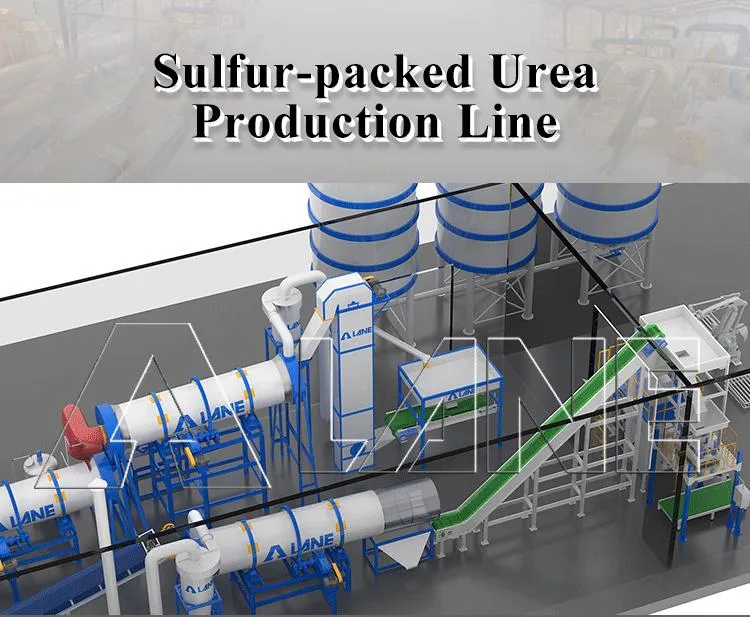
- Outstanding Product Performance: The controlled release fertilizer produced releases nutrients precisely and stably, meeting the needs of different crops.
- Stable and Reliable Quality: Automated control ensures high consistency between batches.
- Efficient and Flexible Production: Can adapt to different formulations, coating materials, and production capacity requirements.
- High Raw Material Utilization: Precise blending and coating reduce waste.
- Highly Intelligent: Reduces manual labor intensity and errors, enhancing management efficiency.
- Environmental Protection and Energy Efficiency: Effectively collects dust and solvents, reduces energy consumption, and meets green production requirements.
- Strong Core Competitive Advantage: Enables fertilizer companies to produce high-end, high-value-added products, securing a competitive edge in the market.
- Investing in an advanced controlled release fertilizer production line is not only an upgrade of manufacturing capabilities but also an investment in the potential opportunities for sustainable agricultural development.
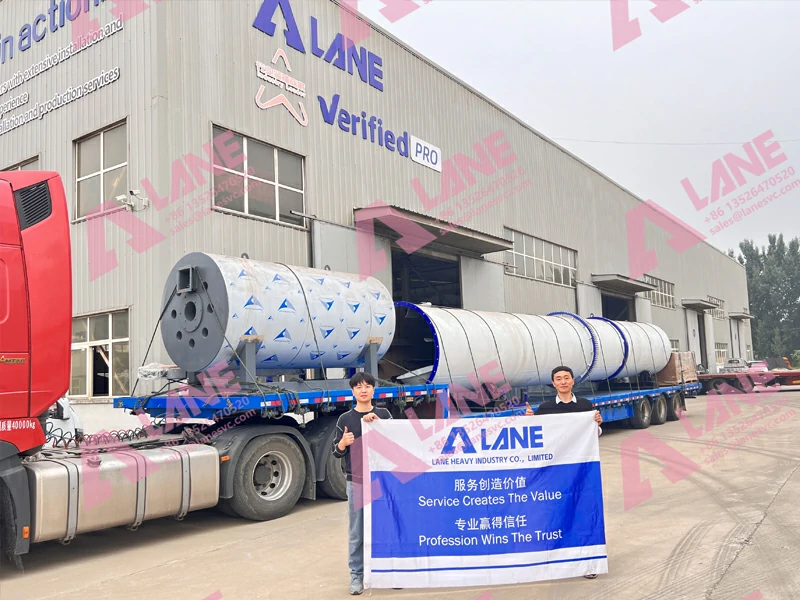
>>>Our Project Map
>>>Youtube Channel